OVERVIEW
A wired glove, developed at the Electronic Visualization Laboratory, University of Illinois, Chicago, in 1977, has been around for about half a century. Despite various versions with new technologies, it hasn’t gained widespread recognition, contrasting with the rapid adoption of the computer mouse in 1973. While there’s no empirical research on this, we can speculate on possible reasons. Before the 21st century, these technologies, even simple sensors, were not accessible. However, cost was also a barrier, much like the early days of the computer mouse, which has now become remarkably affordable. My experimentation involves using five flex sensors, similar to Nintendo’s Power Glove, and an additional gyroscope sensor to capture motions of fingers and hand gestures. The wired glove, along with other novel interfaces, was intriguing at its launch, but its widespread application was not realized at that time.
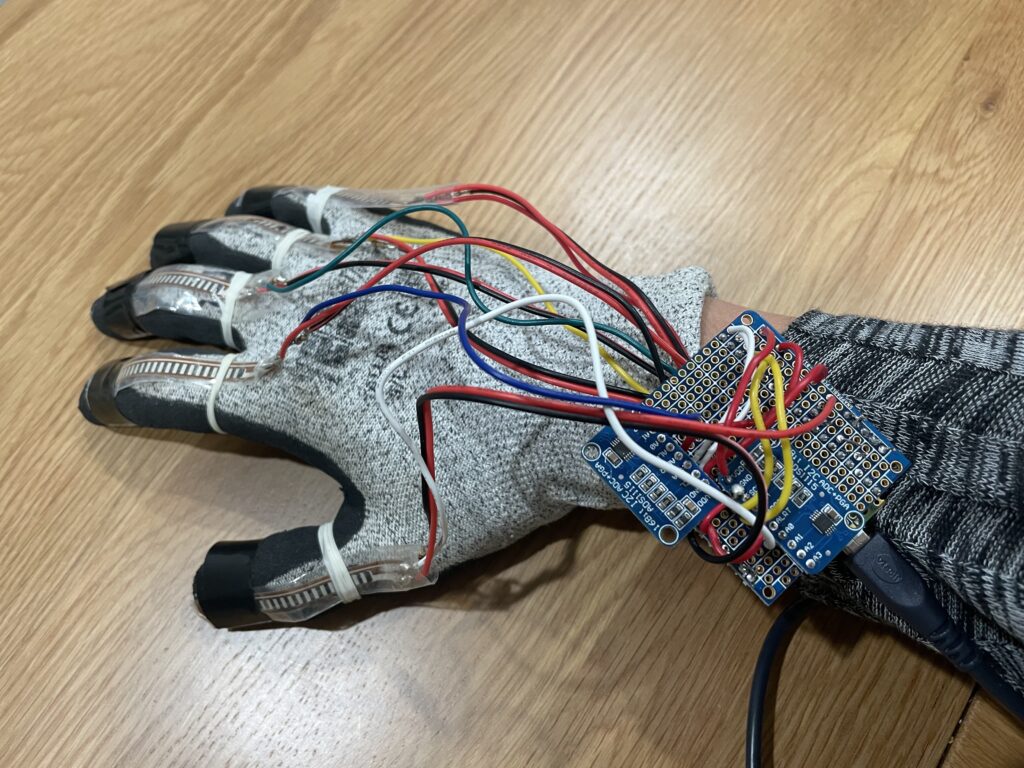
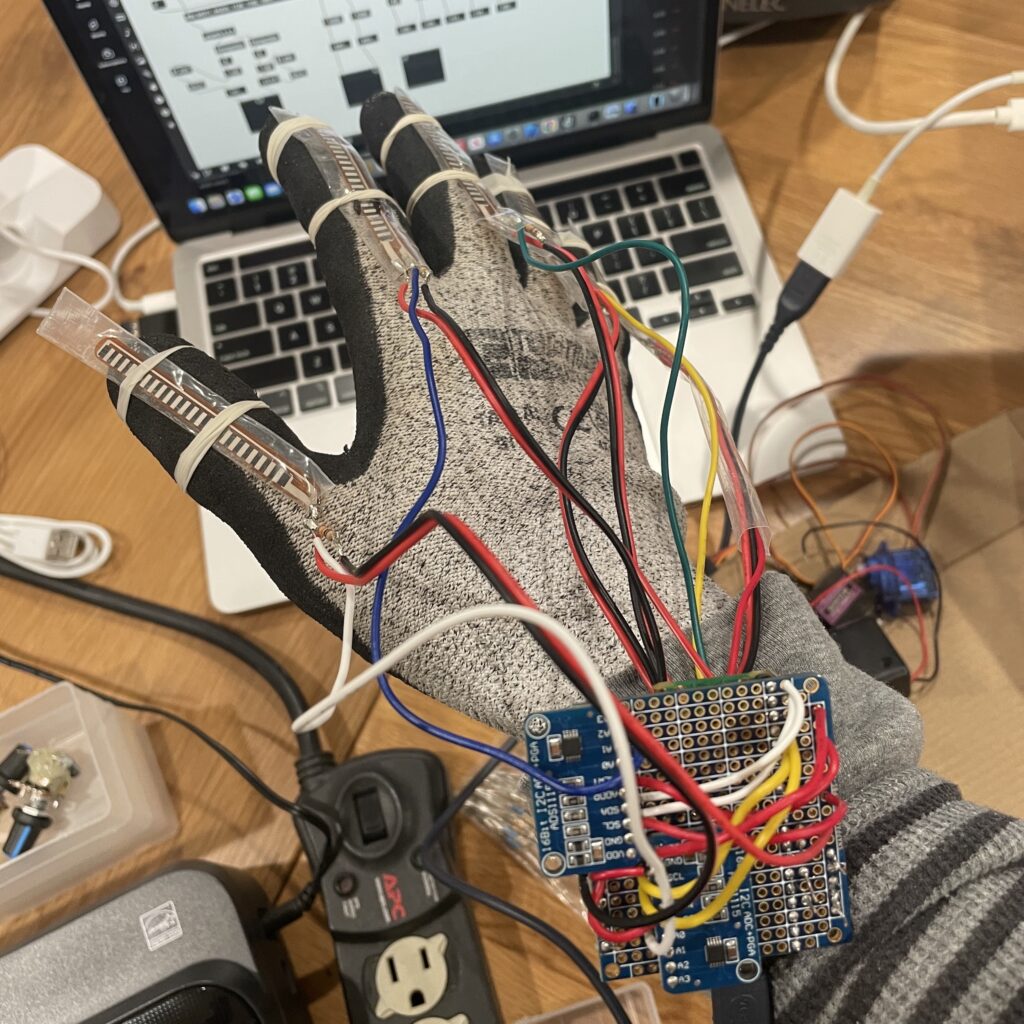
INITIAL PROTOTYPE
The initial prototype, shown above, was assembled using a discarded construction glove, recycled small plastic bags that once contained electronic components, and rubber bands. Since the sensors function as variable resistors, the implementation is straightforward. The flex sensor’s value is sent to the microcontroller (RP2040) through voltage dividers, and the gyroscope sensor transmits motion data to the microcontroller via I2C.
Mounting the sensors and ensuring functionality posed the main challenges. The construction glove, though thick and heavy for protection, hindered flexibility and control. The flex sensor required more space for movement, and its intuitive design wasn’t apparent in the initial prototype, despite all functions working as expected.
REVISED DESIGN
While testing the initial prototype, I found that the glove itself was challenging to control and manipulate. Seeking a more lightweight and flexible alternative, I encountered a new issue. A lightweight and flexible glove struggled to securely hold the sensors, collapsing when the glove was removed. Consequently, a compromise between flexibility and sensor stability needed to be addressed.
To find a solution, we opted to abandon the use of a glove and pursue an alternative design. Another issue with the initial prototype was that if anything broke, most components required disassembly, including the desoldering of electronic parts. I recognized the vulnerability of the sensors and understood that soldering them would be inconvenient and time-consuming, resulting in increased maintenance costs. Consequently, for the new model, we decided to enhance the maintenance aspect as well.
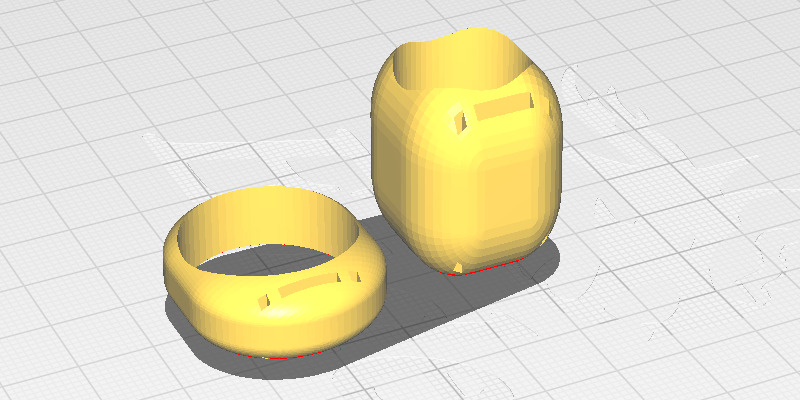
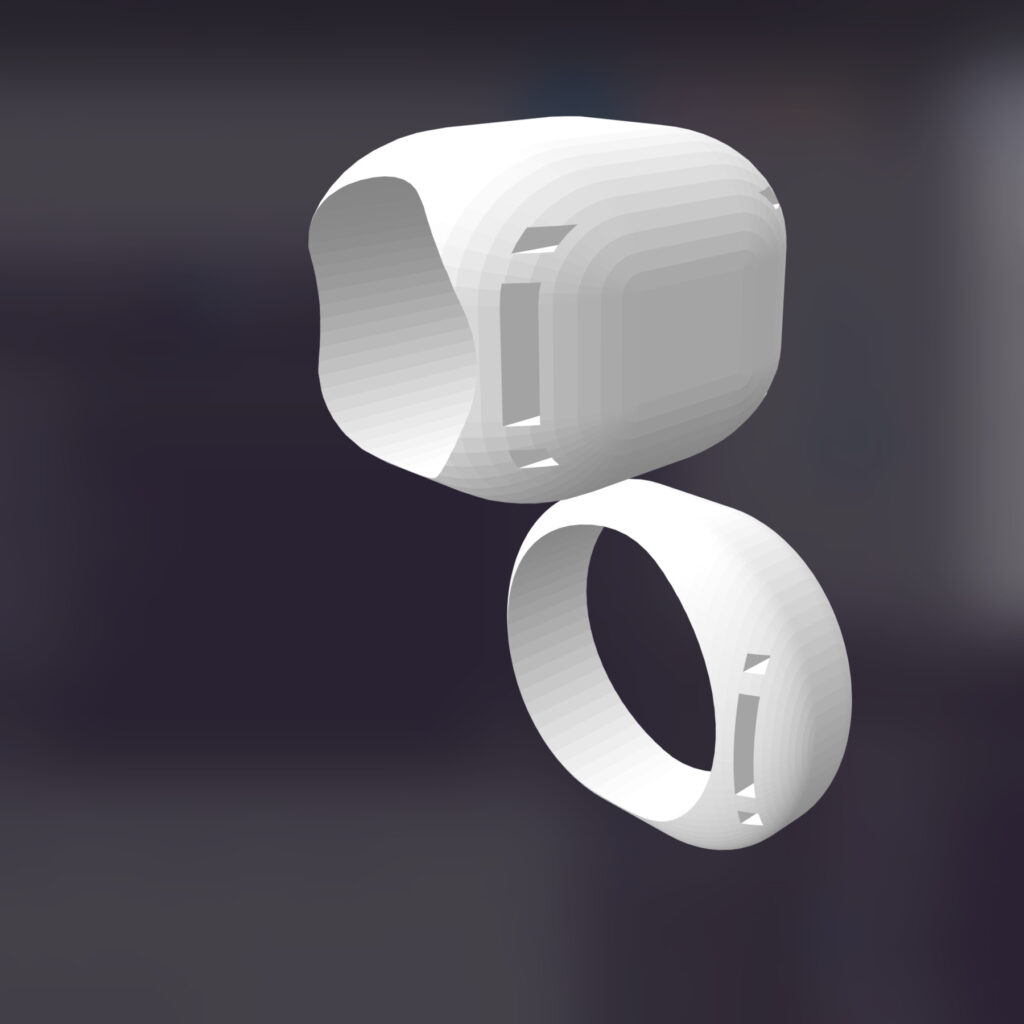
FUTURE PLANS
The new design, adopting ring shapes, enables users to express hand gestures more effectively than the glove. However, I was only able to print the ring on PLA material, which is relatively hard. I plan to utilize different 3D printing materials, such as flexible resin, to enhance user comfort and ensure a more secure attachment to users’ fingers.
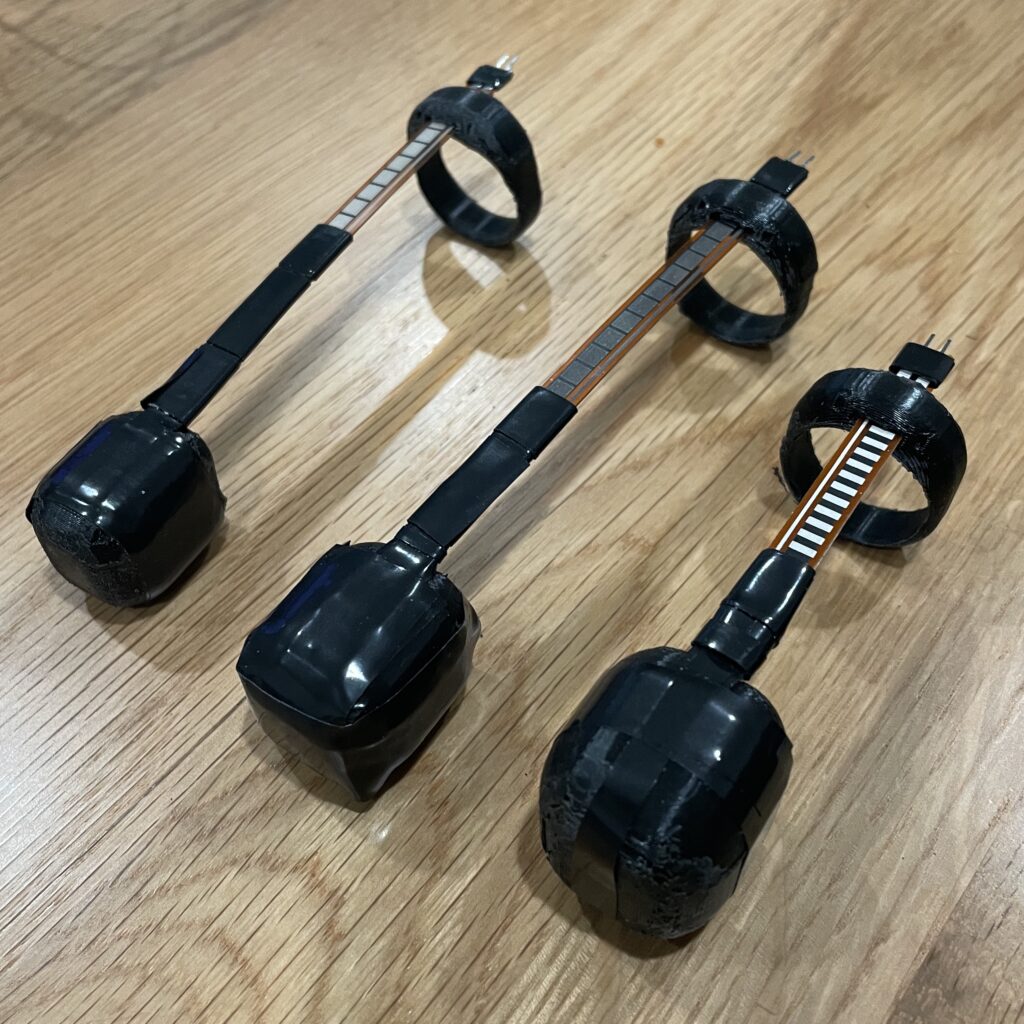
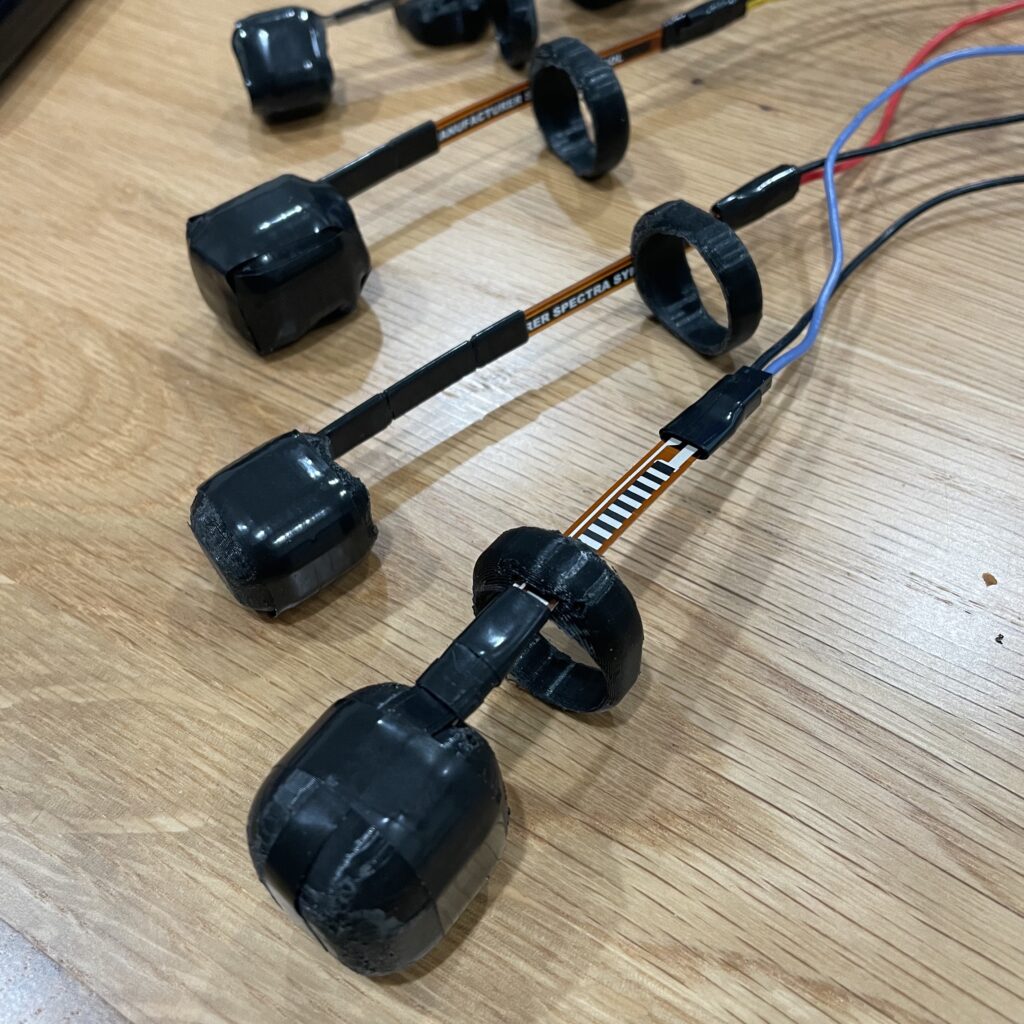
Reply